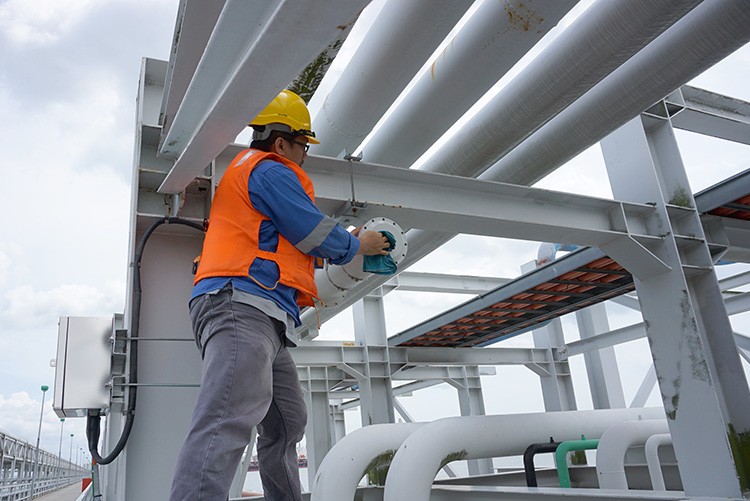
Safe Cable Choices for Hazardous Locations
A major safety concern defined in "hazardous locations" is the occurrence of fires and explosions due to presence of flammable gases, vapors, dusts or fibers. Hazardous locations (HL) are usually found in industrial facilities where explosive liquids, gases or dusts are present. No other aspect of industrial safety receives more attention in the form of codes, standards, technical papers, and engineering design.
Regulatory bodies like the Occupational Safety and Health Administration (OSHA), National Electrical Code (NEC) and the NFPA 70 have established classification systems for locations which exhibit potentially dangerous conditions and hazards. They define the types of hazardous substances that are, or may be, present in the air in quantities sufficient to produce explosive or ignitable mixtures. Hazardous location requirements exist not only to prevent a fire or explosion, but also to contain the fire or explosion should it occur. OSHA provides guidelines for specially designed equipment and special installation techniques must be used to protect against the explosive and flammable potential of these substances.
Hazardous locations are broken into different categories called “Classes” and “Divisions” in NEC’s Article 500 Hazardous (Classified) Locations – Classes I, II, and III, Divisions 1 and 2. The NEC imposes strict requirements for cabling methods in these locations which are permissible by the code-making bodies, also known in the ICT industry as the Authority Having Jurisdiction (AHJ), with safety being the most critical consideration. The “Classes” define the type of explosive or ignitable substances which are present in the atmosphere or could be present. The “Groups” define substances within the Classes and are rated by their flammable nature in relation to other known substances. The “Divisions” apply to the specific conditions and the likelihood of the specific substances in the Groups to exist in the areas.
Class | Groups | Divisions | |
Division 1 | Division 2 | ||
I Gases, Vapors and Liquids |
| Explosive or ignitable gases or vapors are present under normal operating conditions | Explosive or ignitable gases or vapors are NOT normally present (but may accidentally exist) under normal operating conditions |
II Dusts
|
| Combustible dust is in the air under normal operating conditions | Dust is not normally in the air in ignitable concentrations (but may accidentally exist) |
III Fibers and Flyings | Textiles, wood chips, etc. (ignitable but NOT explosive) | Easily ignitable fibers and flyings are handled, manufactured or used | Easily ignitable fibers are stored or handled |
The process of classifying an area is often complex, so it is generally determined by the facility’s engineering staff. Buildings are not classified, but areas within the building are. “Class I, Division 1” is the most hazardous classification. Notice that the ignitables get bigger as the class number increases. Unfortunately, there isn’t always a clear boundary. Often there are areas that have a mix of particle sizes.
Some examples of Class 1 areas are:
- Petroleum refineries, and gasoline storage and dispensing areas;
- Dry cleaning plants where vapors from cleaning fluids can be present;
- Spray finishing areas;
- Aircraft hangars and fuel servicing areas; and
- Utility gas plants, and operations involving storage and handling of liquified petroleum gas or natural gas.
Selecting Proper Cable and Following Best Installation Practices
Each type of hazardous location requires specific types of cable and installation methods. Approved wiring methods range from a rigid, highly impenetrable type of cable, such as Type MI (mineral insulated cable), to a raceway system such as metallic conduit. Cable glands (cable entry devices) used in hazardous locations are intended to provide the safe connection of suitable cables to enclosures, maintaining the explosion protection and ingress properties of equipment. Cable glands provide a degree of environmental and ingress protection required for the equipment they are being connected to and the hazardous location for which they are being installed in. NEC prescribe the requirements for both cable glands and cables.
The NEC defines the types of cables that can be used in hazardous locations, and UL provides the means to approve cables for the US. The various cable types, in conjunction with the appropriate terminations, must provide a system that significantly limits or completely eliminates the possibility of an electrical arc or spark igniting the surrounding flammable gases, vapors, dusts or fibers. The approved cable types range from extremely rigid and impermeable mineral-insulated, metal-sheathed Type MI cables and MC-HL and ITC-HL cables with gas/vapor-tight continuous corrugated metallic sheaths to unarmored, highly flexible Type TC-ER-HL cables and flexible cords.
Cable allowed for use in Class I Division 1 are limited, with a few exceptions, to type MC-HL, ITC-HL, and TCER-HL under special conditions. NEC provides requirements for equipment (including cables) installed in HL areas which includes:
- Identification for use in the Class and Grouping of the location
- Meets specific eternal or exposed surface temperature requirement
- Marked to show its temperature range and the environment for which it has been evaluated
In jurisdictions following IEC requirements, there are product standards for hazardous location cable glands. However, unlike NEC, IEC does not identify specific product standards for hazardous location cables, but provides installation cable requirements according to the IEC 60079-14. And although this standard provides guidance for the minimum requirements for cable installation, it does not define specific tests or construction specifically for hazardous location cable. IEC recommends certain cable properties, such as jacketing materials not to be an “easy tear” type (i.e. with low tensile strength sheaths) unless installed in conduit, jacketing to be extruded and constructed of thermoplastic, thermosetting or elastomeric materials and any fillers need to be water blocking.
Tough Cable Challenges and an Easy Solution
In addition to the cable’s robust construction needed to perform in severe environments, one of the biggest challenges for Ethernet cable is the 100m distance limitations. In harsh environment locations, such as the Class I areas mentioned above, the distances from the telecommunications room (TR) to the devices often exceeds 100m. Adding an additional termination point, whether a telecom enclosure or an additional TR is just not feasible or cost effective.
The GameChanger™ Cable, which was designed to deliver both data and power (PoE) far beyond the Ethernet distance limitations for Category cable, is now available in a version specifically developed for harsh locations. This cable is classified as ITC-HL (instrumentation tray cable for hazardous locations), meeting UL2250 and UL2225 listings for 300V copper conductors for use in Class 1, Division 1 (CI/DI) hazardous locations.
This GameChanger cable consists of 22 AWG copper conductors with FEP insulation and manufactured with an inner jacket covered by a continuously corrugated welded (CCW) armoring and then sheathed with an outer PVC jacket. This cable is ROHS-2 compliant, sunlight resistant and can be direct buried. The operating temperature has a wide range of -50°C to +90°C which assures reliable performance in all severe environments. With the CI/D1 rating this armored cable allows installers to skip the expensive and time-consuming installation of rigid pipe or conduit, and with a reach that goes well over two times traditional cable, saving a significant amount of time and money.
All GameChanger cables deliver 1Gb/s Ethernet and PoE+ up to 656 feet (200 meters) and 10Mb/s Ethernet and PoE+ up to 850 feet making it an ideal pairing for explosion proof cameras, WAPs and other edge devices. This cable eliminates intermediate IDF requirements and the need to install repeaters, power supplies and other equipment, which are costly and introduce additional points of failure.