Industry News
Stay up to date on the latest in intelligent building solutions, and innovations from Paige Datacom Solutions.
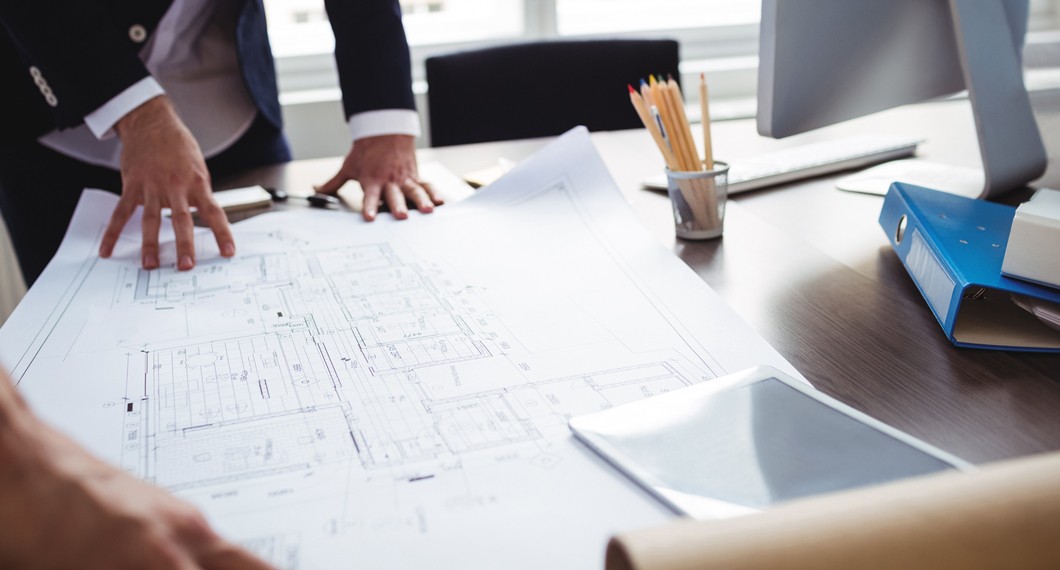
Industry News
Sustainability Starts at the Foundation: Why Future-Proofing Your Cable Infrastructure is the Smartest Green Decision
Discussions around sustainability in networking tend to focus on energy-efficient data centers, low-power equipment, and carbon offsets. But one of the biggest opportunities to reduce environmental impact is often overlooked: the amount of physical infrastructure required to support connectivity.
Latest News
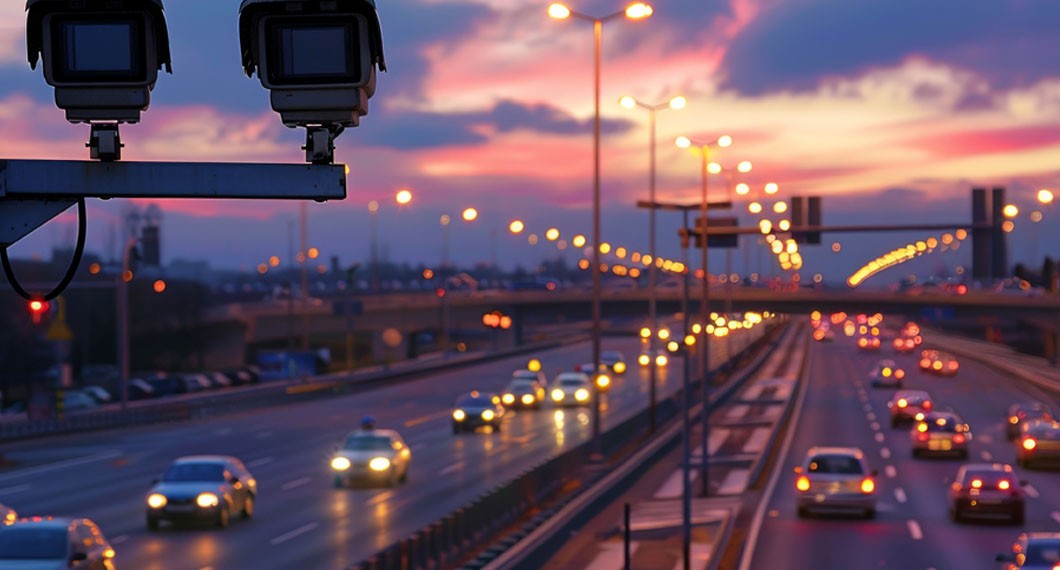
How J.O. Herbert Company Reduced Costs and Failure Points in Intelligent Transportation Systems
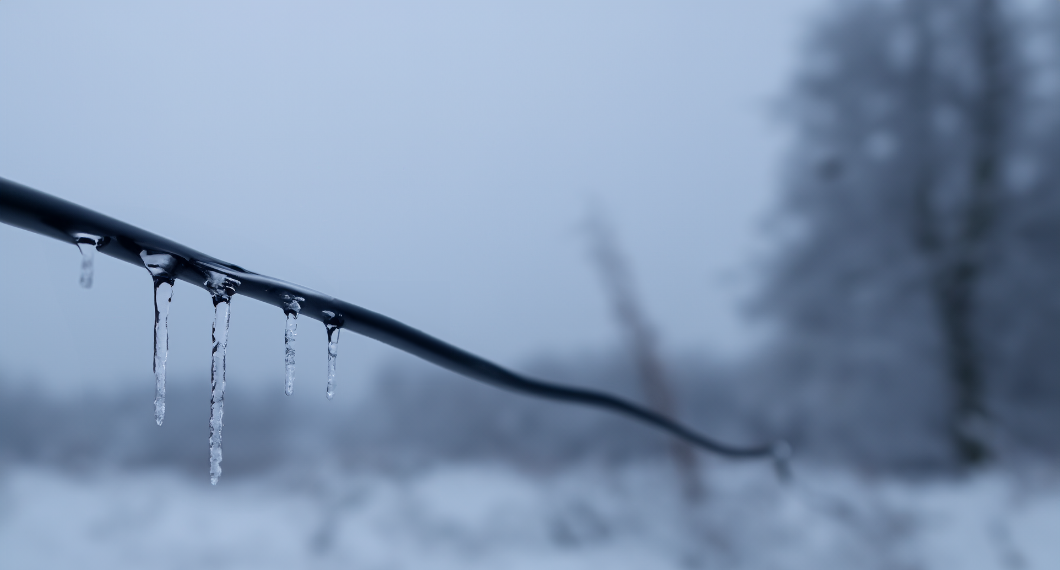
Beyond Freezing: GameChanger Cable's Blueprint for Cold-Resistant Networking

How a Major International Airport Overcame the Distance Dilemma
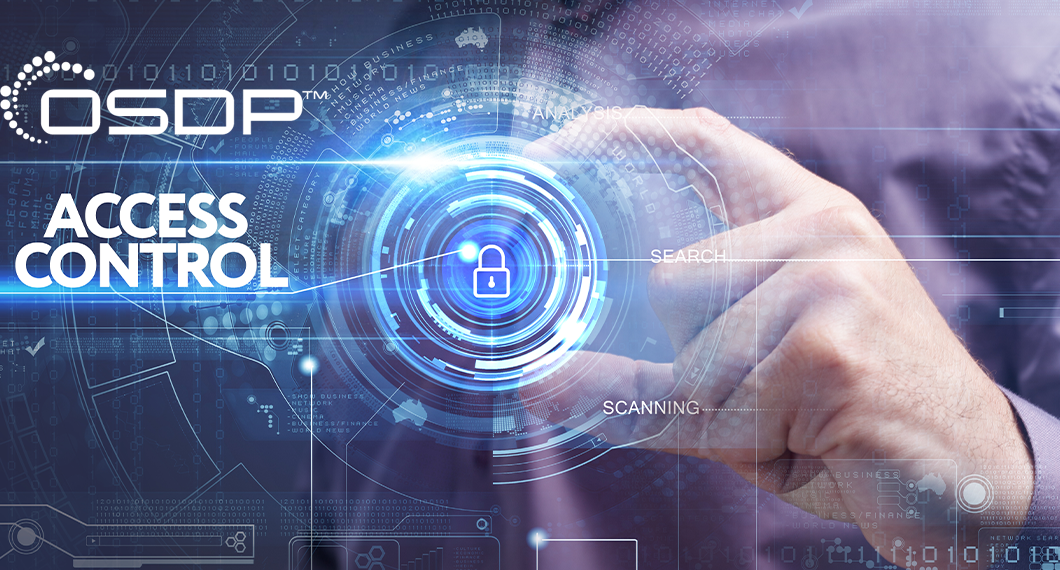
OSDP – What’s the Rush? Why Mat Spears of Presidio Has Made It a Priority
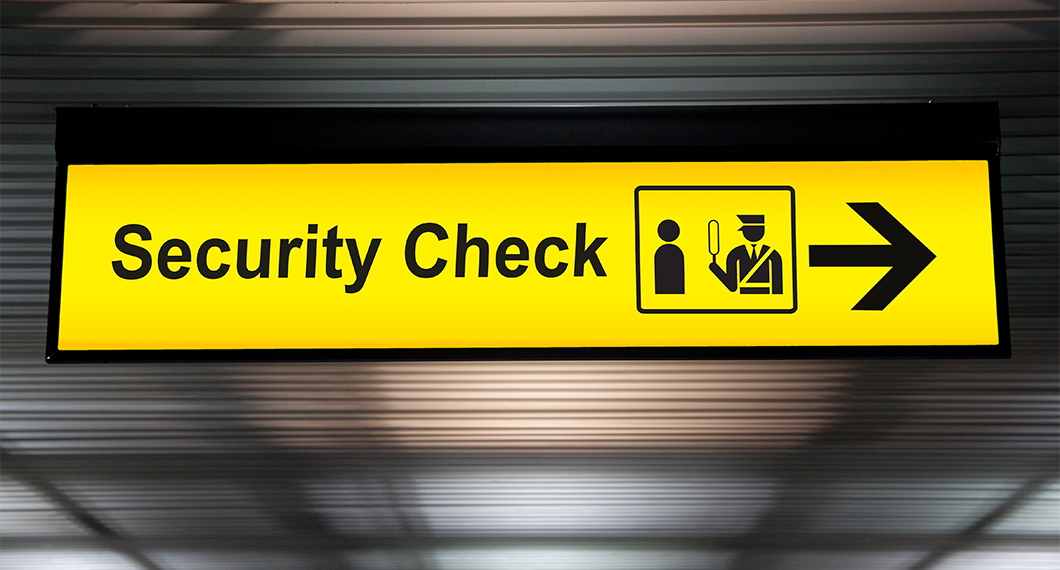
Lengthonomics: A Key Factor in Keeping Airport Costs Down and Security Up
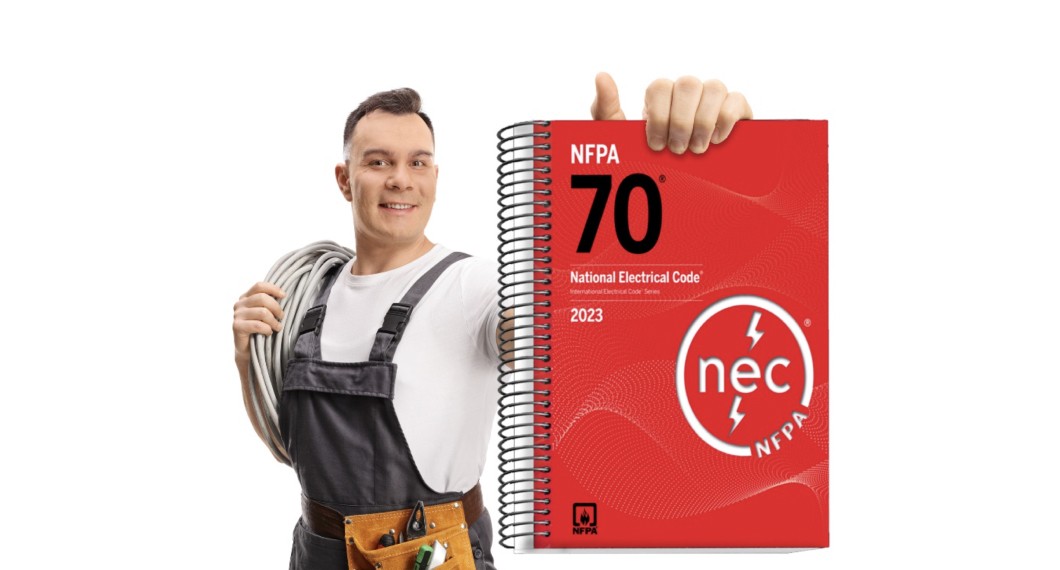
The 2023 NEC® is Here! What You Need to Know
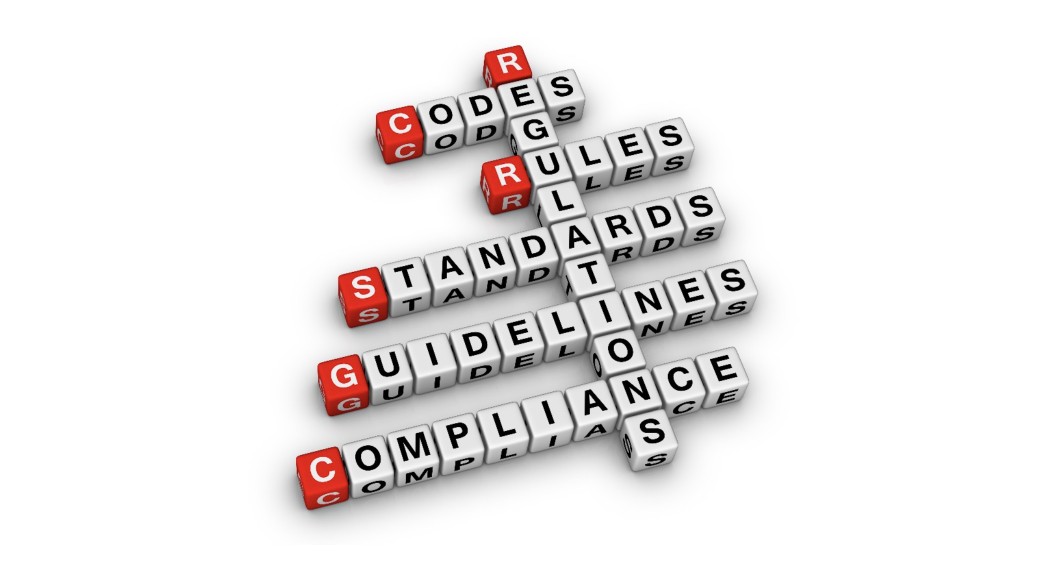
Codes vs. Standards
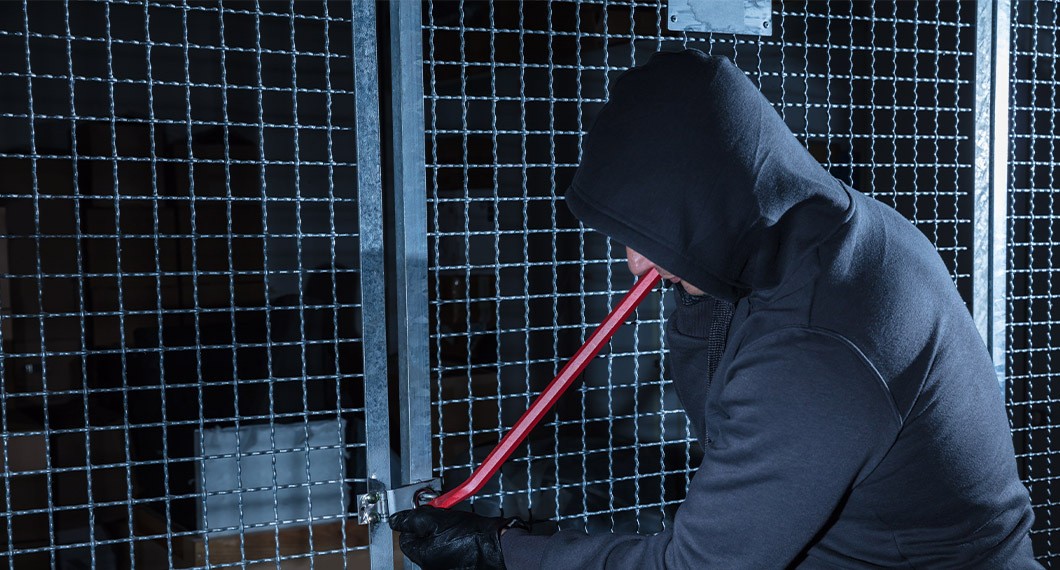
The Holiday Season Is Coming: An Update on Retail Loss Prevention and Asset Protection
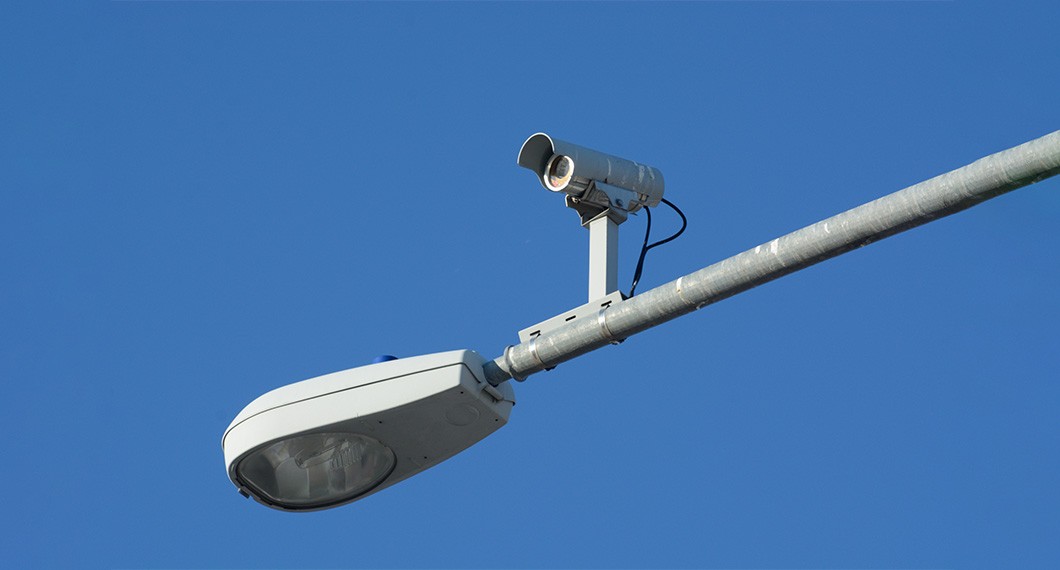